Tungsten Carbide Dies: Powering Precision Manufacturing
In the world of modern manufacturing, tungsten carbide dies play a crucial role, and three types—tungsten carbide wire drawing die, tungsten carbide cold heading forging dies, and tungsten carbide punch die—stand out for their unique applications and significance.
Tungsten carbide wire drawing dies are essential in the wire production industry. Their exceptional hardness and wear - resistance properties ensure that during the wire drawing process, where metal wires are gradually reduced in diameter, the die can maintain its shape and precision over extended periods. This not only guarantees the consistent quality of the drawn wires but also reduces the frequency of die replacement, improving production efficiency.
Tungsten carbide cold heading forging dies, on the other hand, are designed to withstand the high - pressure and impact - intensive environment of cold heading and forging operations. When manufacturing components like bolts and nuts, these dies can precisely shape the metal under cold conditions. Their high fatigue resistance allows them to endure repeated forging cycles, ensuring the mass production of high - quality fasteners with accurate dimensions.
Tungsten carbide punch dies are indispensable in sheet metal processing. Whether it's creating holes or cutting out complex shapes in metal sheets, these punch dies offer excellent cutting performance. Their ability to resist wear ensures that the edges of the punched or cut parts remain sharp and burr - free, which is critical for the subsequent assembly and functionality of metal products.
Overall, tungsten carbide wire drawing die, tungsten carbide cold heading forging dies, and tungsten carbide punch die are the backbone of many manufacturing sectors. Their superior material properties make them the go - to choice for achieving high - precision, high - quality production, and driving forward the progress of the manufacturing industry.
Type 12、13 、S11、S13 Carbide drawing die nibs
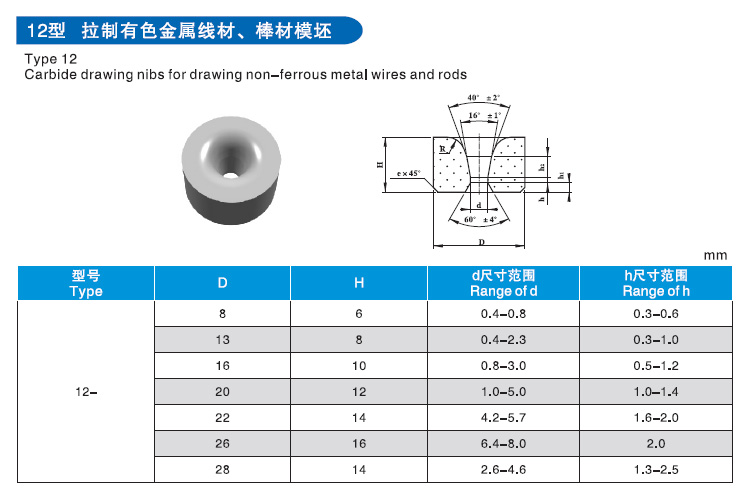
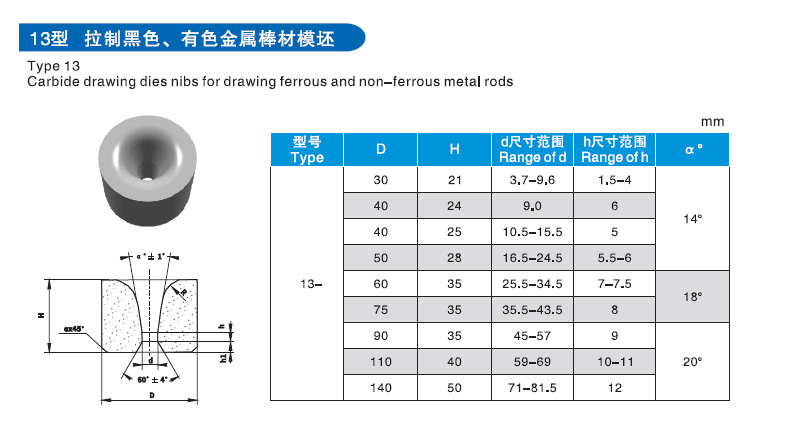
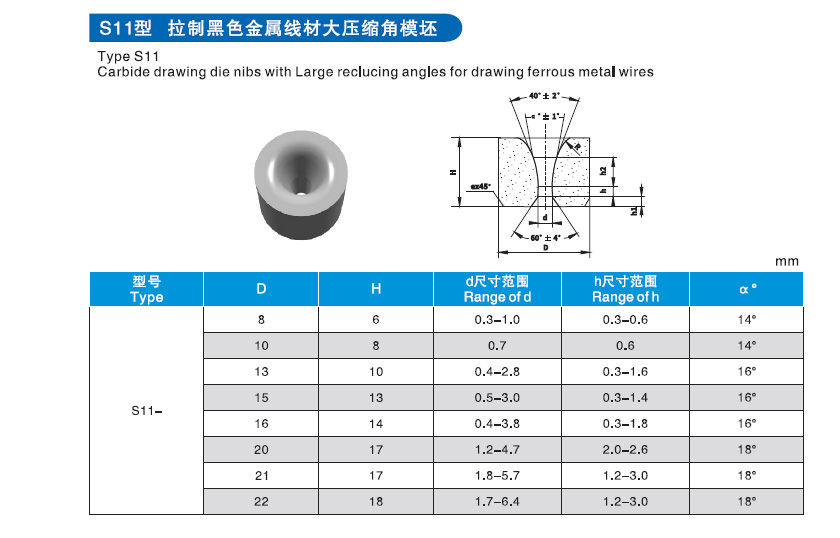
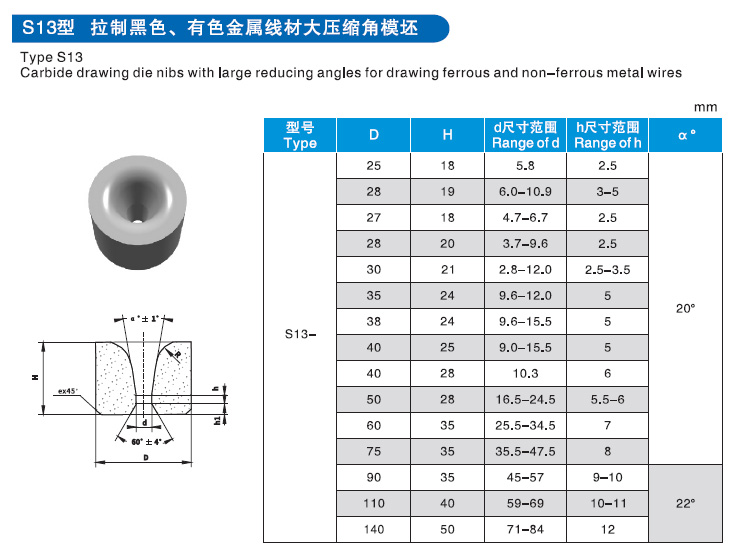
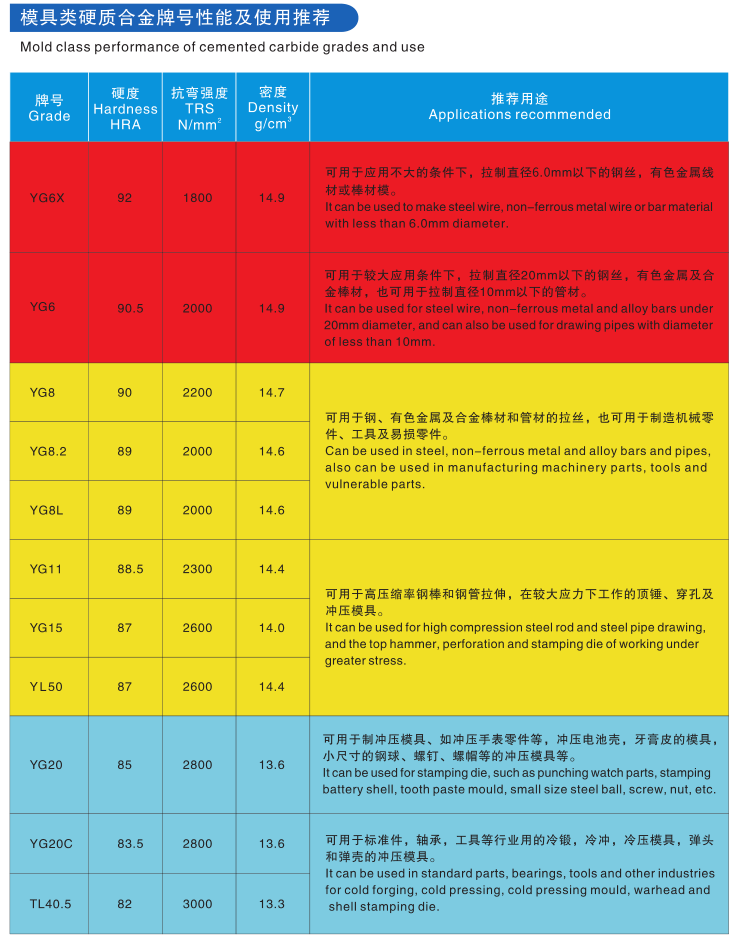