Product name : End Mill Cutter
Product No. : End Mill Cutter
Details:
Exploring High-Quality Carbide End Mills: A Powerful Tool in Metal Processing
In the field of mechanical processing, the performance of cutting tools directly affects processing efficiency and product quality. Carbide end mills, as widely used cutting tools, stand out among numerous tools due to their excellent performance, and high-quality solid carbide end mills are even more outstanding.
Carbide end mills are made of cemented carbide. Cemented carbide is formed by sintering high-hardness refractory metal carbide powder and binder at high temperature, endowing the end mills with properties such as high hardness, high strength, and good wear resistance. It can efficiently complete milling tasks on various metal materials, such as steel, cast iron, stainless steel, and even high-hardness titanium alloys. It is widely used in operations like face milling, grooving, chamfering, and contour milling.
Solid carbide end mills, with both shank and cutting edge made of cemented carbide, have significant structural advantages. On one hand, they have extremely high rigidity, are not easy to bend during cutting, and can ensure high-precision processing. The processing tolerance can be controlled within a very small range, meeting the processing requirements of precision parts. On the other hand, due to the consistent overall material, they can withstand higher cutting speeds and feeds, maintaining stability under high-speed cutting and greatly improving processing efficiency. For example, in mold manufacturing, where high precision is required for cavity and core processing, solid carbide end mills can play a significant role in accurately shaping complex shapes and ensuring mold quality.
High-quality solid carbide end mills integrate cutting-edge manufacturing processes and high-quality materials. In terms of materials, fine-grained or ultra-fine-grained carbides are selected to further enhance hardness and toughness. The application of coating technologies, such as TiAlN coatings, improves the tool's wear resistance, heat resistance, and chemical stability, extending its service life and reducing processing costs. In terms of manufacturing processes, advanced CNC machining technology is used to ensure the dimensional accuracy and geometric consistency of the tools, optimize the sharpness and durability of the cutting edges, make cutting smoother, and reduce the surface roughness of the processed workpieces.
In automobile manufacturing, the processing of key components such as engine blocks and transmission housings requires high-quality solid carbide end mills to ensure precision and production efficiency. In the aerospace field, the demand for lightweight and high-performance components has promoted the use of these tools in cutting difficult-to-machine materials such as titanium alloys and superalloys, contributing to the manufacturing of aerospace parts.
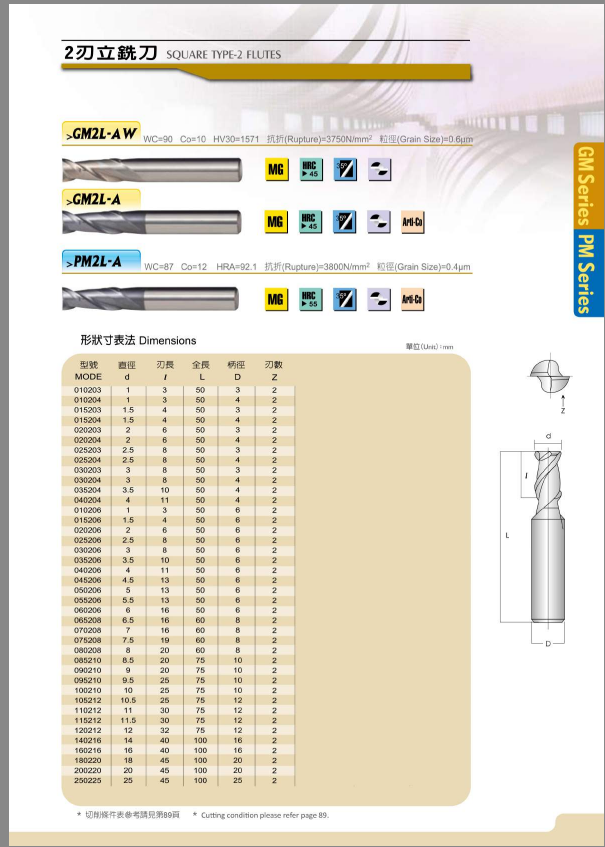
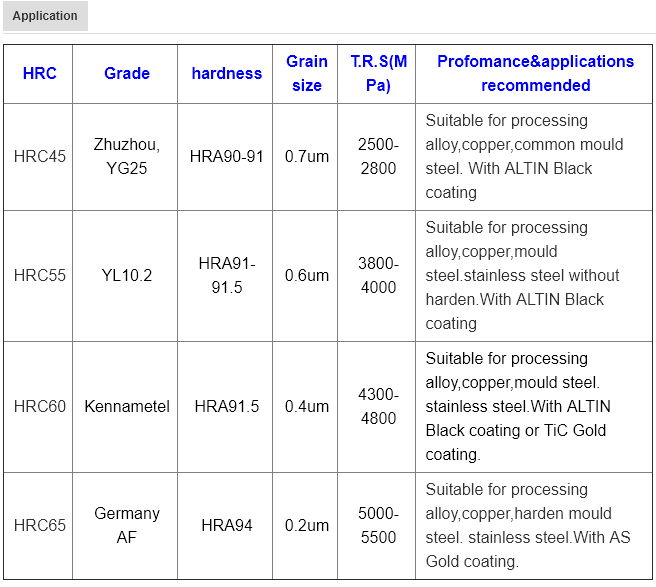